INTERSTATE HEAVY EQUIPMENT - NORFOLK
Operating the motor graders is not easy, and other extensive construction equipment, like excavator and backhoe loader. This necessitates a thorough understanding of the equipment and a specific skill set to do the jobs efficiently and accurately.
Many operators regarded the motor graders as the most challenging trucks to operate among heavy equipment. This is because they are a little different from the others in setting the controls, such as the blade's angle and height, which necessitates a certain level of competence, especially when setting them to get an acceptable degree of the result.
Yes, motor graders are a little odd to run, but they aren't that difficult. Working with precision measures is a requirement for every machine, whether a motor grader, excavator, or backhoe loader. It is necessary to have good training and expertise behind the controls and comprehension of the equipment and its different pieces to achieve results that completely match the desired level.
Motor Graders Decoded
Motor graders are typically great for mixing concrete, placing patches, expanding shoulders, cutting back slopes, ditching, scarifying, drying material, and removing snow. However, before getting into the motor grader recommendations, it's crucial to understand what a motor grader is and how it works.
The purpose of a motor grader is to level or smooth out an area. They have a long wheelbase that traverses small depressions or humps. Motor graders usually have a blade in the middle that you can tilt to cast out on either side. The mouldboard is the portion of the grader that is for cutting, mixing, windrow, and dispersing material. The circular section of the motor grader, i.e., the circle, is attached to the mouldboard with the cutting blade. Using the mouldboard, you can modify the blade for height, angle, pitch, and reverse orientation. The blade angle is the angle of the blade regarding the mainframe, which is usually 180 degrees or a straight line. With the frame, the mouldboard forms angles.
Let's look at some guidelines for operating the motor graders to help you get the most out of your machine after you've mastered the fundamentals.
1. It's critical to understand how to position the mouldboard properly. It would be best to keep the mouldboard straight up and roll the grader blade forward to soften the edge. This also improves back visibility, allowing the operator to operate more quickly.
2. To avoid rolling over, keep the mouldboard parallel to the front axle, centralized to the frame, and lowered close to the ground when tearing across a slope.
3. You can modify the motor grader's moldboard in various ways. Operators raise and lower the mouldboard by a fraction of an inch to adjust to finish grading. The more earth that spills down the heel, the greater the angle of the mouldboard.
4. Operators should utilize mouldboard angles of 10 to 30 degrees for light and free-flowing materials; you should use greater mouldboard angles of 30 to 50 degrees for moist and sticky materials when mixing giant windrows and requires ditching.
5. It's not a good idea to articulate a motor grader when operating on steep slopes because the grader can roll over, causing severe bodily harm or death.
6. When cutting out washboards, articulating the rear frame toward the toe of the mouldboard by 2 to 5 degrees helps lessen the tendency of motor graders to bounce.
7. When using the ripper, drop the teeth into the ground while moving the grader. If the ripper loses traction in the back wheels, the operator must raise the ripper until the wheels regain traction. It would be best to minimize the number of teeth on harsh surfaces, lower the teeth under the pavement, and lift the ripper to shatter old pavement.
8. The operating speed significantly impacts the quality of work produced by motor graders. As a result, the machine travel speed should be kept as high as possible for maximum production. It should, however, be kept low enough to avoid machine bounce (generally 3 to 5 mph).
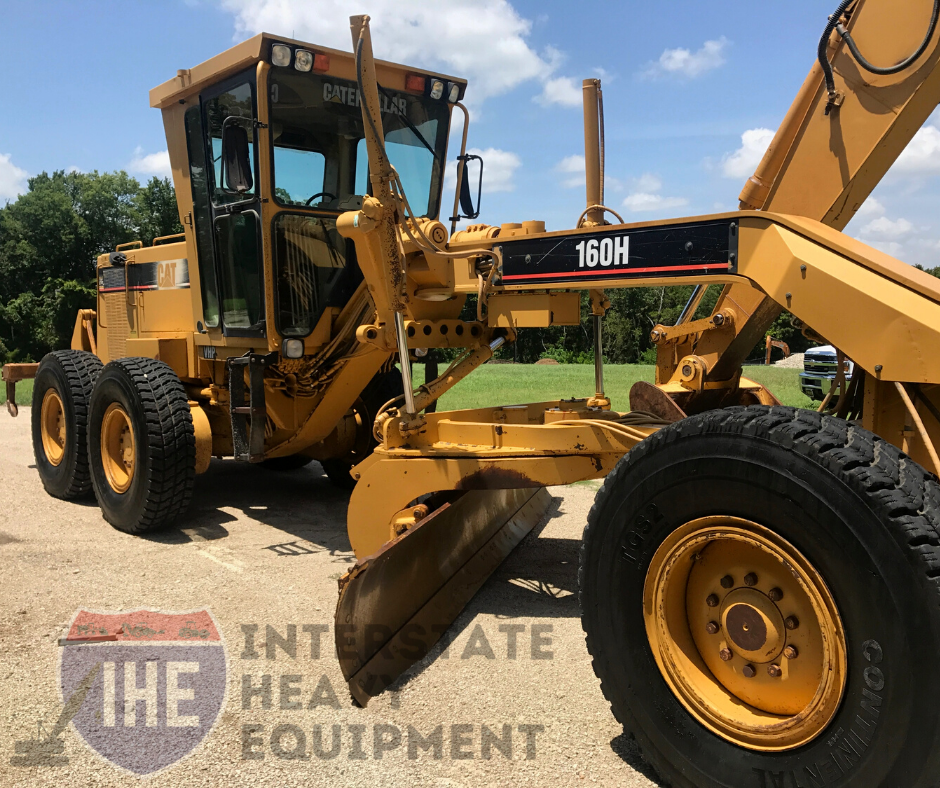
9. All motor graders have control levers that allow them to change the position of the mouldboard, and a thorough understanding of these controls is critical.
10. When turning the motor grader around, the wheels should always be pointing in the direction of the turn. This will make it easier for the motor grader to turn.
11. Only the necessary downward pressure should be given to complete any operation. Excessive downward pressure on a hard, dry surface will cause rapid cutting-edge wear, use more horsepower and fuel, and lower productivity.
12. When working, keep an eye on both ends of the blade because elevating one end can cause the other end to drop about a quarter of the distance.
13. If the circle is not perfectly level, the blade set may change when the blade angle changes.
14. You can pitch the blade slightly forward to cut soft material and somewhat backward for mixing, laying operations, and cutting hard surfaces. You can also pitch it forward for spreading or retaining surface material and snow removal.
15. When removing snow, drive straight and never apply so much down pressure that the front wheels are elevated to the point where steering is rendered useless.
These are only a few of the many available tips for operating the motor graders, and the list is extensive. Although based on the preceding steps, one might conclude that motor graders are the most challenging heavy equipment to run, this is not the case. Motor graders require a basic understanding of the equipment and some prior expertise. When it comes to running them, they are comparable to other equipment.
Source: Mahindra