INTERSTATE HEAVY EQUIPMENT - LAS CRUCES
The United States utilizes heavy machinery on almost all construction projects. Heavy construction equipment is required to build and maintain the nation's infrastructure, from massive road projects to residential homebuilding, and remaining safe by following heavy equipment safety tips when working with heavy machinery is critical.
Working with or around extensive construction equipment instills a healthy respect for the heavy machines' capacity. You need to know what your equipment can do, whether you're working with a vast excavator on a commercial construction site, a grader in the road building sector, or a skid steer on a domestic restoration project. That includes the things it can do to you.
Heavy construction equipment can be deadly when operated incorrectly. Still, most employees go about their regular tasks without getting hurt because they are aware of the risks connected with equipment operating and take precautions to avoid mishaps. These savvy operators and assistance well understand the necessity of heavy machinery safety.
THE VALUE OF SAFETY IN HEAVY EQUIPMENT
No one can overstate the importance of heavy equipment safety. According to the Occupational Health and Safety Administration (OSHA), the construction sector is one of the most dangerous industries in America. The record shows there were 4,693 workers killed on the job in 2016. Furthermore, 21.1 percent of those deceased, or 991 workers, were killed on construction sites. One out of every five construction workers in the United States perished on the job.
According to OSHA, construction workers died and injured themselves for four main reasons. These are known as the "fatal four" because they account for two-thirds of all fatal accidents. According to OSHA, removing the fatal four unintentional causes would save the lives of around 631 American employees each year. The following are the four deadly accident causes:
Falls accounted for 38.7% of worker deaths, with falls from a height or construction equipment accounting for the rest.
Struck by an Object: 9.4% of construction workers died due to being struck by an object on the job.
Electrocutions: 8.3 percent of construction worker deaths were caused by being accidentally electrified by electricity.
Caught In-Between: In the United States, 7.3 percent of construction workers perished due to being caught between components of construction machinery or materials.
In collaboration with state and local partners, OSHA shifted its focus from enforcement-based safety to educational support. As a result, American worker fatalities have decreased from 38 per day in 1970 to 14 per day in 2016, thanks to the combined efforts of government regulators and private entities like companies, unions, and safety experts.
Heavy equipment safety tips were a priority for everyone in the construction sector. They also resolved to act and improve working conditions on building sites. Workers were educated and given thorough safety instructions as part of this. One of the most important goals was to remove, mitigate, and lessen hazards for people who work with heavy machinery.
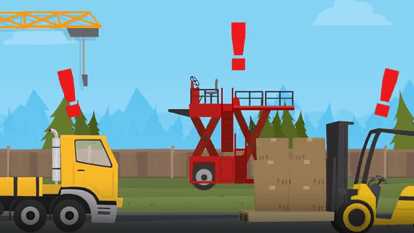
RISKS OF WORKING WITH HEAVY EQUIPMENT
While falls and electrocutions are the most common construction-site injuries, being struck by objects and caught between mechanical components and materials is more common in heavy machine operations than in typical site conditions. Therefore, mitigating potentially unsafe conditions and making all personnel aware of their status are vital to preventing or minimizing equipment-related injuries.
Workers' attention and knowledge of their job site surroundings are called situational awareness. There are three main concepts to follow for defining and recognizing job site dangers. First, all workers must be aware of the following hazard categories:
1. Mechanical Dangers
There are moving parts in all heavy construction equipment. The threat comes from the energy stored in machinery parts and releasing it. Most machines are relatively stable and safe when not in use. However, they have tremendous power and can cause severe damage while operational.
When working around equipment, keep an eye out for moving parts that could cause injury. Machinery and equipment that can release debris and hit someone can also be hazardous. Rotating shafts, colliding surfaces, scissor or shear action, sharp edges, and detachable connections are common mechanical risks. Entanglement, crushing, severing, cutting, and puncturing are all mechanical risks, as are slips and falls when dodging moving components.
2. Hazards that aren't mechanical
Components in motion are not the only source of severe equipment risks. Almost every machine has a reserve of energy. Examples are gases or fluids under pressure, electrical charges, and hot surfaces. Non-mechanical dangers to workers include unpleasant chemicals such as exhaust emissions and chemical by-products. Consider the noise pollution that heavy machinery operations cause.
Workers that are situationally aware always check their machinery for non-mechanical hazards. They are aware of how heavy machinery impacts the surrounding region or environment. Non-mechanical risks include:
Dust
Environments that are explosive or flammable
High-intensity light radiates and conducts heat, such as lasers or welding arc flashes.
Lead, mercury, and cadmium are examples of heavy metals.
Releases on Steam
Microwaves and X-rays are examples of ionizing radiation.
Burns, lung damage, and long-term elevated risk of cancer-related disorders are among the health dangers posed by non-mechanical hazards.
3. Dangers of Access
Many industrial injuries and deaths occur because workers have unsafe access around machinery paths. Workers become accidentally imprisoned and exposed to mechanical and non-mechanical hazards when they do not have safe access to and from a specific spot. Proper design, putting in protections, and boosting workers' situational awareness can help them avoid being stuck between harmful components or struck by objects.
Consider who is allowed into a dangerous place or scenario and what equipment and materials are in use when it comes to reducing access dangers. Rather than reacting to an unanticipated scenario, access control must be anticipated and prepared ahead of time. The most effective way to reduce access-related accidents is to communicate all mechanical and non-mechanical heavy equipment hazards adequately.
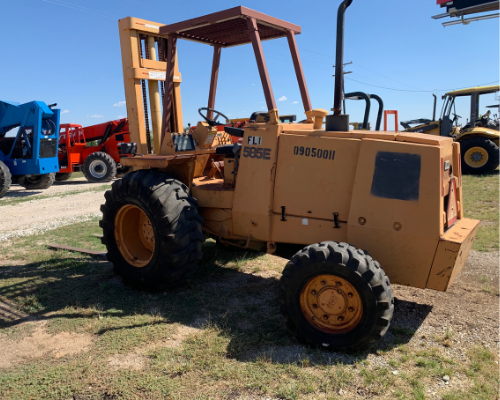
SAFETY OF COMMUNICATION AND HEAVY EQUIPMENT
Hazard mitigation entails a set of instructions for dealing with potentially risky events. You can avoid hazards if possible, or at the very least, replace them with something less harmful. If this isn't achievable, industries must implement risk controls to prevent or limit the risk of harm or injury. Workplace health and safety standards require communication between workplace risks and risk controls. According to the law, workers must use hazard communications in the "highest order."
High-order risk controls send out safety warnings right away. Non-mistakable signage that indicates existing hazards and prescribes safe procedures for personnel exposed to them are examples of high-order communication.
Lower-order hazard controls explain the safety precautions that workers must take when working near potentially risky equipment.
For example, a lower-level communication approach prescribes the appropriate personal protective equipment and specifies safe workplace actions such as de-energizing equipment and shutting out activation devices.
The hazard communication order chain includes administrative controls. For example, standard operating procedures include complete instructions for safe operation and exposure reduction. Another successful method of administrative control for accident prevention is verbal communication, such as toolbox meetings.
Many organizations employ administrative controls to disseminate safety information to employees. Adequate safety procedures include personnel at all levels, from equipment operators to those who work in their immediate vicinity. Giving safety guidelines and emphasizing the necessity of heavy equipment safety improves situational awareness.
SAFETY ADVICE FOR CONSTRUCTION EQUIPMENT
It is everyone's responsibility to stay safe when working with extensive machinery. Sharing knowledge about heavy equipment safety tips is also essential. The most excellent firms with the finest safety records have a corporate culture that emphasizes safety as a core value. They've created a reputation for safety through a behavioral-based strategy that encourages employees to commit to safety rather than comply with legislation.
Safety-conscious cultures encourage all employees to recognize potential hazards and work together to eliminate them. They make all workplace hazards known and educate workers about the dangers of construction machinery.
Identifying and controlling job site dangers is a continuous activity. As work advances, situations on the job site frequently change, and it's critical to communicate changing conditions. However, there are many instances where workers expose themselves to the same hazards daily. Here are some tried-and-true safety recommendations for anyone working with big machinery:
Keep yourself out of the line of fire.
This tip is a top-of-the-line safety recommendation. Every location around a piece of heavy equipment where a worker could get caught in-between or hit by a mobile object is called the line-of-fire. Both the operator and the ground worker enforce the line-of-fire regulation. There must be clear communication between the machine operator and the workers surrounding them about what they want to perform.
Make eye contact with the other person. It is vital to maintain eye contact with a heavy equipment operator for safety reasons. Both the operator and the surrounding workers are aware of each other by making eye contact. This step prevents a machine or material from swinging at a stationary worker who might approach the line of fire.
Make good use of communication signals. Radio communication between machine operators and support employees is every day on construction sites. Knowing what others are doing and communicating changes in operation is critical for safety, and there is no better method than vocal communication. Radios, on the other hand, are not infallible. Presenting hand signals is a fail-safe communication method.
Have spotters on hand. Many construction equipment operators use spotters, including those who operate excavators, delivery trucks, and cranes. There are blind areas on every machine when the operator is visually challenged. Using a ground spotter is a high-value insurance policy against moving equipment or materials into potentially unsafe positions by accident.
Determine a hazard zone and mark it.
Construction sites openly show hazards to anyone near construction equipment by marking a danger zone. The danger zone is where the line of fire begins and ends. Construction industries use barriers, fencing, or caution tape to restrict the risk zone. However, it's also practical to use simple signs that clearly explain the safety boundaries.